Today we traveled to the Bullseye Glass Company in Portland. This company is known for making large sheets of artisan glass of many different colors, and what is called frit which is basically crushed for glass projects. All of this glass is compatible with each other, so if you melt them together they won’t break. We use this glass back at school for glass projects so it is interesting to be able to see where it comes from. We were there all day, doing two workshops and getting a tour of the actual factory itself.
After a long introduction about the glass revolution in the States and Bullseye’s involvement in different glass developments over the years, we got into making sugar skulls! We packed frit and super fine frit (powder) into molds of sugar skulls. We used powder that was mixed with water and gum agar (natural acacia tree resin) to create our designs. We were also able to make our own stencils and sift powder over them to create the shapes we wanted. We had to tamp down our base color over our designs very tightly so that the shape would hold well. After that, we added sand as another layer to our compacted frit to help allow the glass to heat evenly when put in the kiln.
After a quick bag lunch we began a tour of the factory! In two groups with our safety glasses on, we began by looking at the area where hot molten glass is scooped out with essentially a large shovel about 6 feet long that can hold 15 pounds of glass and is ran over to a table where glass is pressed out like fresh pasta in thin sheets then heated in an oven and sent through a conveyor out to quality control. We also saw the potatoes which are stirred into the glass to release the bubbles that can’t escape via steam from them burning in the molten glass.
After the casting line, we saw the line where they make clear sheets. In this line, they make very large sheets of glass that are about 8 or 9 feet. With such a large sheet of glass, they had to use a very big ladle. This ladle has to have 2 people to work it. One uses a scoop, and one basically wheels it around since it is so heavy. It can hold about 200 pounds of molten glass. The ladle is wheeled over to a machine that works the same as the casting line. After being flattened into a sheet, it is pushed into an annealer which helps slowly cool the glass so it does not crack.
Next we saw the quality control area. The sheets from earlier are now cooled and while they were an ocean blue when hot, they are now a bright marbled purple! They are inspected with special glasses and a light that will shine a rainbow through the sheet if there are any imperfections such as bubbles or fractures. They are cut to size and stacked for shipments. The pieces cut off are sorted and prepared to become frit.
Next, we saw the shipping warehouse and then the architectural concept room. In the warehouse there were just many wooden boxes full of personal orders for people that were ready to be put on trucks and shipped out. In the architectural concept room, they work on big pieces that are commissioned for places like churches, and hotels, and anywhere that would like a beautiful piece of “stained glass” art. They take the image that is going to be created and make a grid on it to blow it up to size. The designs are created using frit, stringers (glass rods) and multi-colored sheets, which are put in large kilns and then hung together when finished to create the image.
Lastly, we worked on personal plates where we practiced cutting glass. While seemingly simple it was hard to get straight lines. We used special cutters with a smelly oil and a straight edge. After the practice, we began our plates. Many students creatively cut different shapes such as triangles and made different designs and patterns in the glass. We worked on also making sure our glass would be correctly trimmed and shaped to fit our clear cover. Everyone had a really great time and results.
Click here to view all of the 2020 ECS blogs.

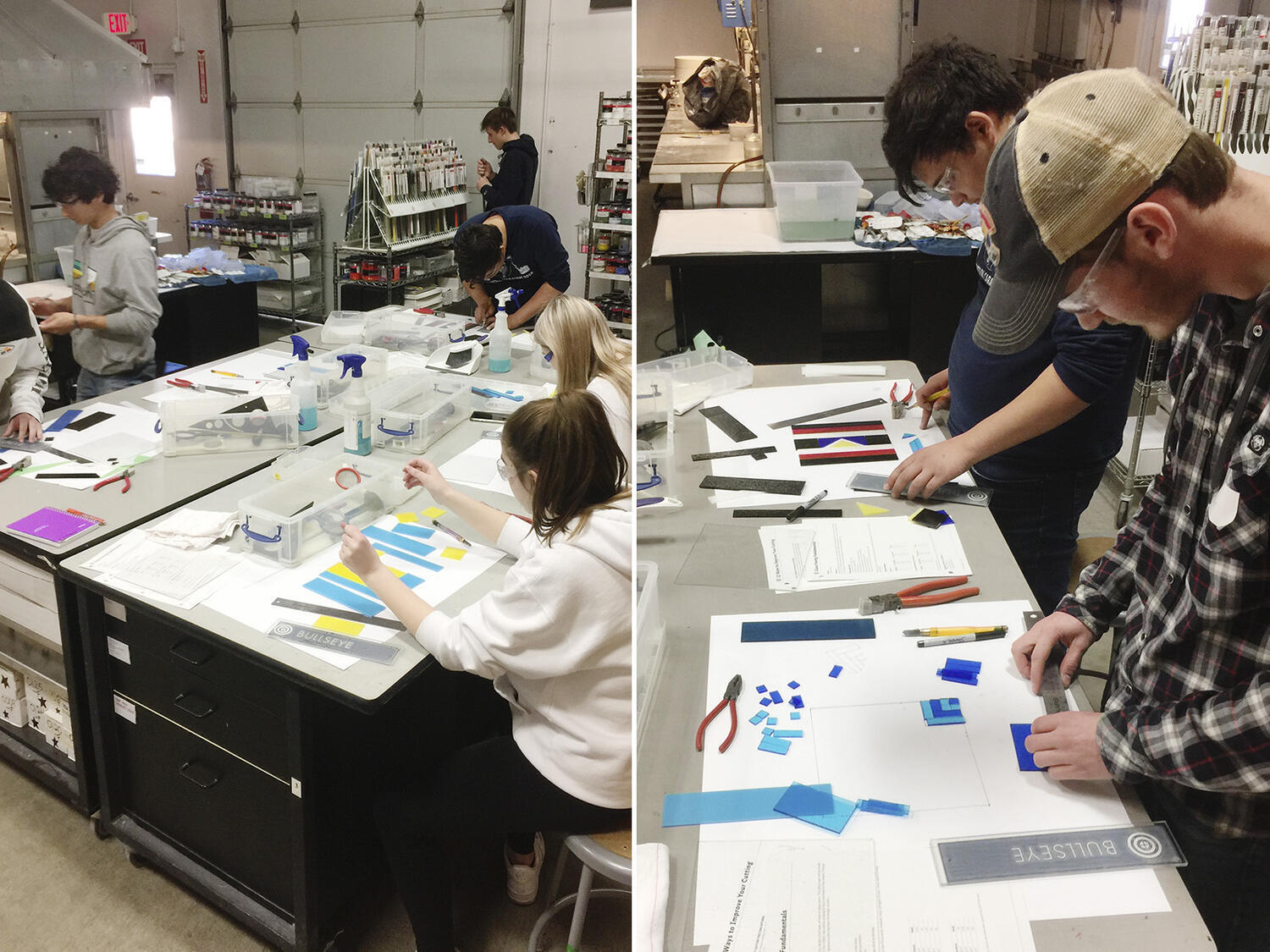